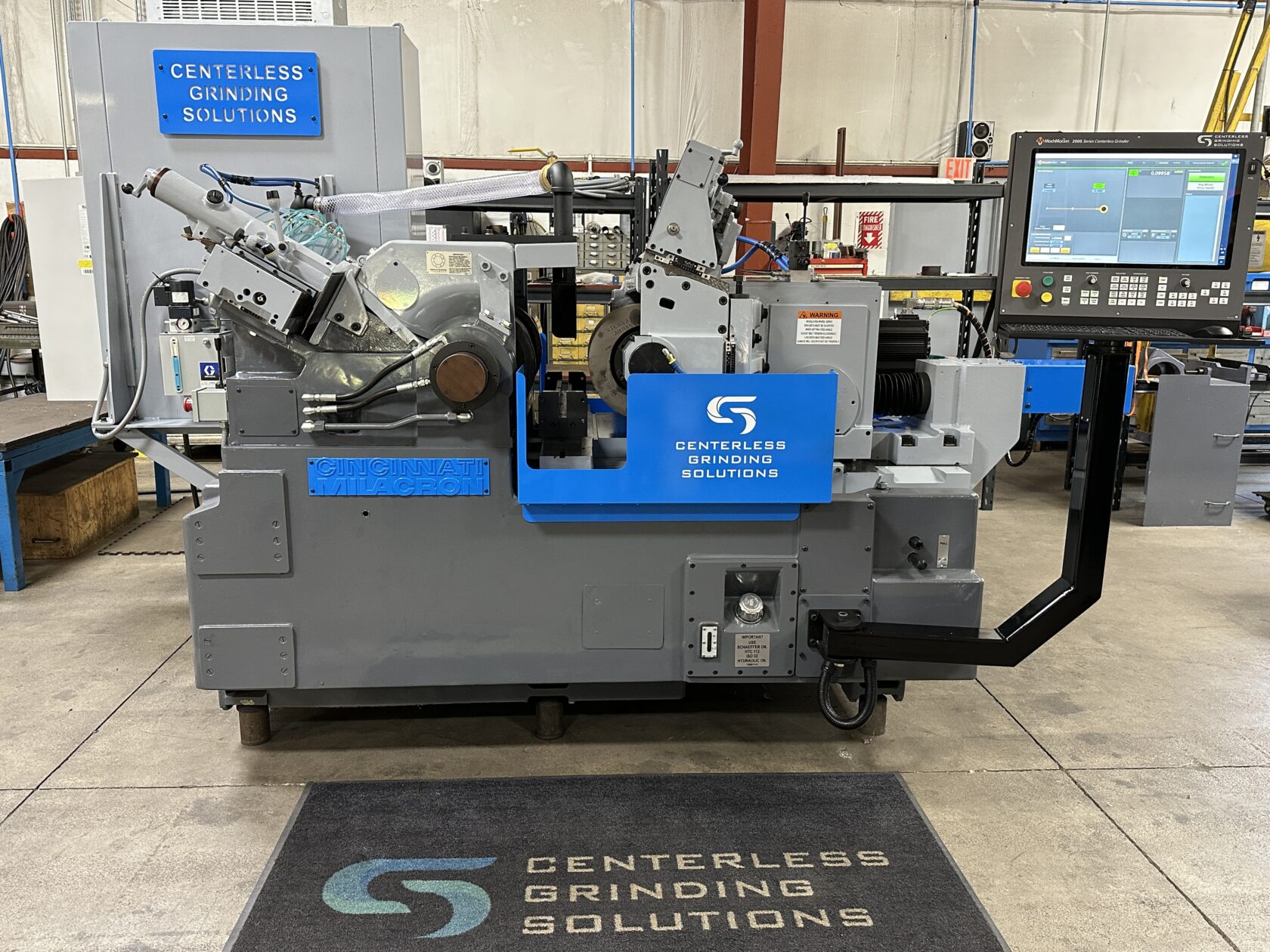
Comparing Centerless Grinding to Other Grinding Methods
When selecting the optimal grinding method for precision manufacturing applications, understanding the differences between centerless grinding and other grinding techniques is crucial for achieving superior results. Centerless grinding offers unique advantages that make it the preferred choice for high-volume production and specific geometric requirements, though other methods may better suit certain applications.
What is Centerless Grinding?
Centerless grinding is a machining process that removes material from cylindrical workpieces without using centers or chucks to hold the part. Instead, the workpiece rests on a work rest blade between two grinding wheels: the grinding wheel that removes material and the regulating wheel that controls the workpiece rotation and feed rate. This method enables continuous processing of parts with exceptional roundness and surface finish quality.
Key Advantages of Centerless Grinding Over Traditional Methods
Superior Production Efficiency
Centerless grinding significantly outperforms other grinding methods in high-volume production scenarios. Unlike cylindrical grinding that requires individual part setup and clamping, centerless grinding enables continuous through-feed processing. Parts can be loaded and processed without stopping the machine, resulting in cycle times that are often 50-75% faster than conventional grinding methods.
The elimination of setup time between parts makes centerless grinding ideal for production runs exceeding 100 pieces. While other grinding methods require operators to position, clamp, and align each workpiece, centerless grinding maintains consistent positioning through the work rest blade and regulating wheel system.
Enhanced Geometric Accuracy
Centerless grinding produces superior roundness compared to other grinding methods because the process naturally corrects geometric imperfections. The workpiece floats between the grinding wheel and regulating wheel, allowing the grinding action to eliminate out-of-roundness conditions that might be locked in by chucks or centers in other grinding processes.
Surface finishes of 4-16 Ra are routinely achievable with centerless grinding, often surpassing the capabilities of cylindrical or surface grinding methods. The consistent contact between the workpiece and work rest blade provides stable support throughout the grinding cycle, minimizing vibration and chatter that can degrade surface quality.
Centerless Grinding vs. Cylindrical Grinding
Cylindrical grinding uses centers or chucks to hold workpieces while a grinding wheel removes material. This method offers advantages for complex geometries and longer parts but presents significant limitations compared to centerless grinding.
Workholding Differences: Cylindrical grinding requires precise workholding setup for each part, while centerless grinding supports parts naturally through the work rest blade system. This fundamental difference impacts both cycle time and geometric accuracy.
Part Length Limitations: Cylindrical grinding can handle longer parts more easily, making it suitable for shafts and rods exceeding 12 inches in length. Centerless grinding typically works best with parts having length-to-diameter ratios under 10:1, though specialized techniques can extend this capability.
Setup Complexity: Centerless grinding requires more initial setup expertise to establish proper wheel speeds, work rest blade height, and regulating wheel angle. However, once optimized, the process runs with minimal operator intervention. Cylindrical grinding offers simpler initial setup but requires individual part positioning for each cycle.
Surface Grinding Comparison
Surface grinding removes material from flat surfaces using a horizontal or vertical spindle grinding wheel. While effective for flat surfaces and specific applications, surface grinding cannot match centerless grinding’s efficiency for cylindrical parts.
Application Scope: Surface grinding excels at flat surface preparation, slot grinding, and angular surfaces. Centerless grinding specializes in cylindrical surfaces, making it the superior choice for rods, pins, tubes, and similar round components.
Production Volume: Surface grinding typically requires individual part handling and positioning, limiting production rates compared to centerless grinding’s continuous feed capability. For high-volume cylindrical parts, centerless grinding offers substantially higher throughput.
Internal Grinding Applications
Internal grinding removes material from internal diameters using specialized grinding wheels and techniques. This method serves applications that centerless grinding cannot address but offers different advantages and limitations.
Geometric Capabilities: Internal grinding handles bore diameters, internal tapers, and complex internal geometries that are impossible with centerless grinding. However, it cannot achieve the external surface quality and production rates possible with centerless grinding for external cylindrical surfaces.
Tooling Requirements: Internal grinding requires specialized grinding wheels, spindles, and often complex fixturing. Centerless grinding uses standard grinding wheels and relatively simple tooling, reducing complexity and maintenance requirements.
When to Choose Alternative Grinding Methods
Despite centerless grinding’s advantages, other methods may be preferable in specific situations:
Complex Geometries: Parts with shoulders, keyways, or non-cylindrical features often require cylindrical grinding or other methods that accommodate workholding fixtures.
Very Long Parts: Shafts, rods, or tubes with extreme length-to-diameter ratios may exceed centerless grinding capabilities, making cylindrical grinding the better choice.
Low Volume Production: For prototype work or small batch sizes under 25 pieces, the setup time for centerless grinding may not justify its use compared to simpler cylindrical grinding approaches.
Internal Features: Parts requiring internal grinding operations obviously cannot use centerless grinding for those surfaces, though external surfaces might still benefit from centerless grinding in a multi-operation process.
Optimizing Your Grinding Method Selection
Successful grinding method selection requires evaluating multiple factors including production volume, part geometry, tolerance requirements, and surface finish specifications. Centerless grinding excels when roundness, surface finish, and production efficiency are primary concerns for cylindrical components.
Consider part handling requirements, as centerless grinding’s through-feed capability eliminates much of the material handling associated with other grinding methods. This reduction in handling not only improves efficiency but also reduces the risk of part damage during processing.
Tolerance capabilities vary between methods, with centerless grinding typically achieving tighter roundness tolerances while other methods may excel at specific dimensional characteristics. Understanding these trade-offs helps optimize process selection.
Making the Right Choice for Your Application
The decision between centerless grinding and other grinding methods depends on your specific application requirements, production volume, and quality objectives. For high-volume production of cylindrical parts requiring exceptional roundness and surface finish, centerless grinding offers unmatched advantages. However, complex geometries, internal features, or specialized applications may benefit from alternative grinding approaches.
Working with experienced centerless grinding specialists helps ensure optimal method selection and process optimization. Professional evaluation of your specific requirements, including part geometry, material considerations, and production goals, provides the foundation for successful grinding method selection and implementation.